Single Point Diamond Turning (SPDT)
Single Point Diamond Turning (SPDT) is an Ultra-precision Machining Process, which delivers surfaces with Form Tolerances within Sub-Micron Accuracies & Roughness within few Nanometers
HOW SPDT IS ACHIEVED?
SPDT Process is a Near-Ideal combination of: Precision Diamond Tool of Designated Geometry, Controlled Precision Turning Operations, Deterministic Material Removal, Meticulous Machining Protocols, Detailed Dimensional Metrology and Accurate Surface Characterization
WHY SPDT IS REQUIRED?
- To Develop Optical Surfaces with Sub-Micron Form & Figure Error and Single Digit Nanometric Finish
- To Deliver Near-Theoretical Optical Performances
- To extend the Optical Performances from Spherical to Non-Spherical Surfaces
- To Develop Systems with Budgets on Weight, Volume & Foot-Print
- To Deliver Neo-Compact Precision Modules.
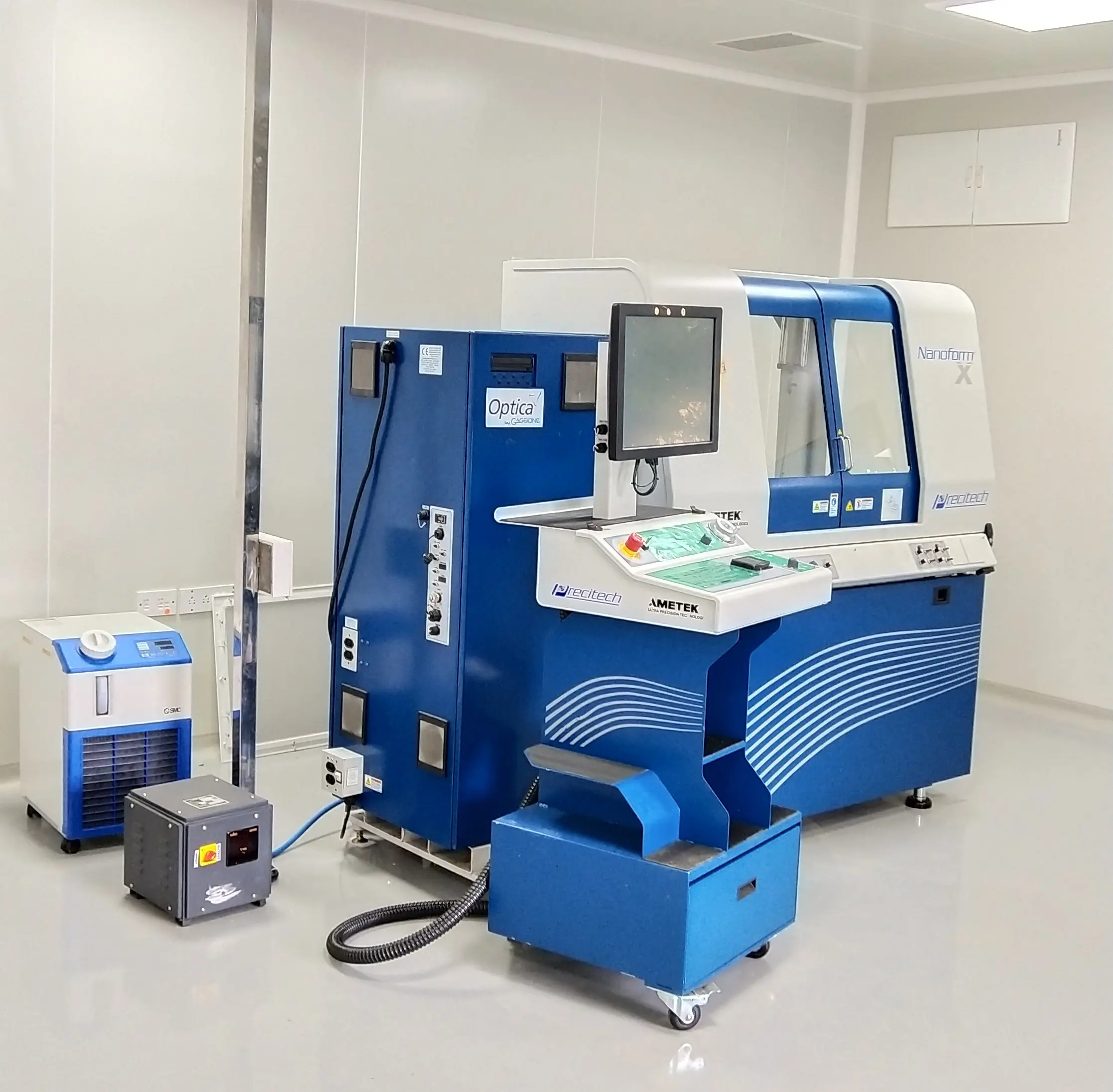
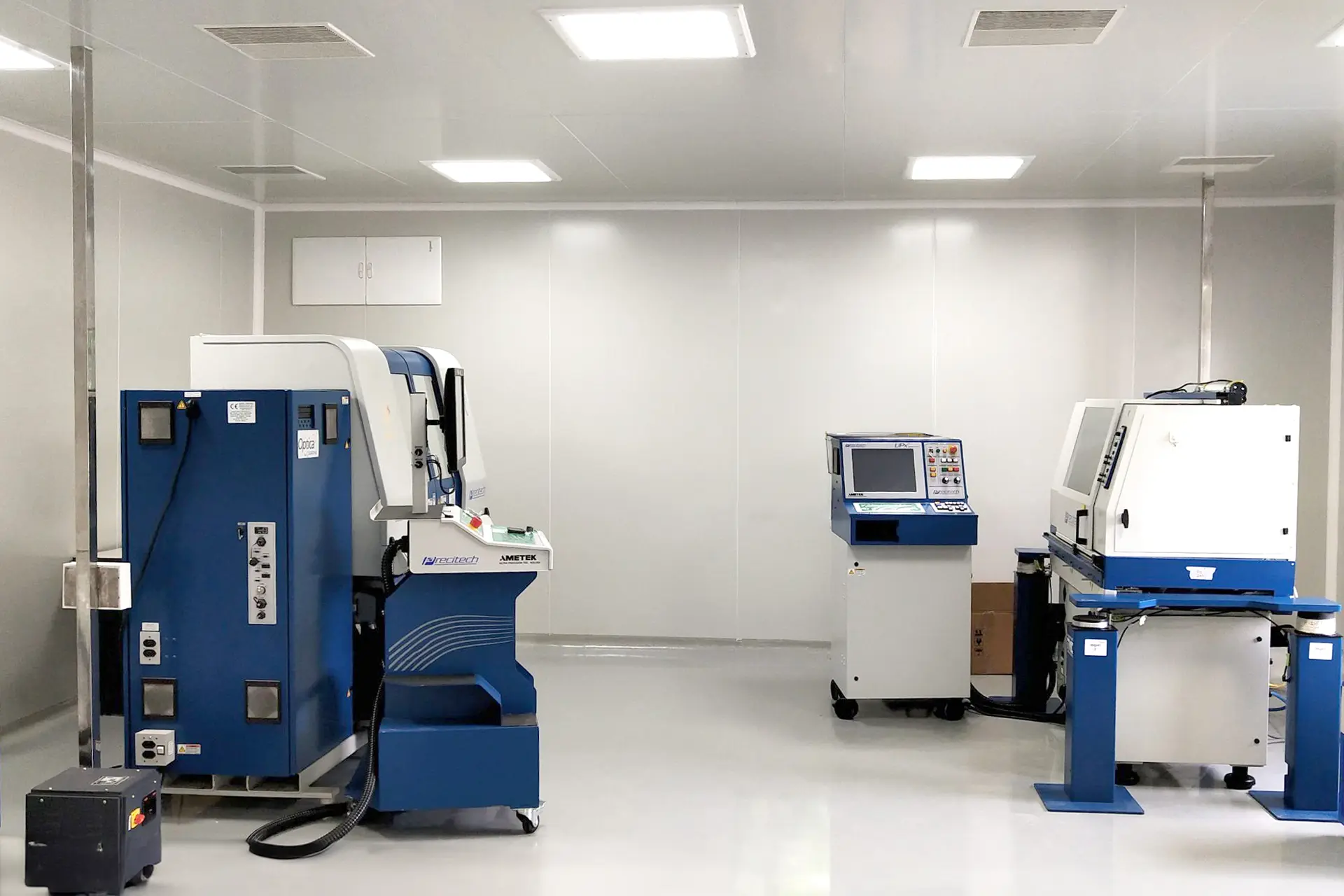
CAPABILITIES:
At the Diamond Turning Facility of OPTICA the following Optical Profiles can be developed:
- Flats
- Rotationally Symmetric Conic Profiles (Spherical, Oblong Elliptical, Prolate Elliptical, Parabolic, Hyperbolics)
- Off-Axial Components
- Toric Surfaces (with Fast & SlowTool Servo Accessory)
- Lenslet Arrays
- Freeform Surfaces with limited definitions
- Ultra-High Precision Mechanical Modules with definable geometries
Metals:
Non-Ferrous Metals, Aluminum & Al-Alloys, Brass, Bronze, Copper & Cu-Alloys, Nickel, Electro-less Nickel, Tin, Antimony, Silver, Low-Carbon Steels & Special High-HRC Steels
IR Materials:
Germanium, Silicon, Calcium Fluoride, Zinc Sulphide, Zinc Selenide, Chalcogenide Glasses and IRG-Series
Polymers:
PMMA, Poly Carbonate, (COP) Cyclo Olefin Polymer (ZEONEX etc), Polystyrene, Poly Ether Imide, ULTEM etc.
Shapes Processed:
Circular, Elliptical, Square, Rectangular, Multi-Sided etc.
SURFACE PROFILE QUALITY PARAMETERS:
The surface quality of the Diamond Turn-generated profile depends on the Substrate Material, Workpiece Geometry, Precision Diamond Tools deployed, Design specifications, Work-piece Applications, Operating conditions etc.
At OPTICA, we routinely develop surface profiles with better than one wavelength Power (Form) Error, λ/3 – λ/10 (PV) Figure Error, λ/20 – λ/50 (RMS) Figure Error and Finish within 2-10 nm (Ra) of Roughness.
The Profile surface quality can be tailored as per the customers’ requirements.
FACILITIES:
- Full-Fledged Mechanical Workshops with NC, CNC Precision, (Turning/Milling).
- Fully Equipped Optical Workshops.
- Thin Film Coating Facilities (AR, High Reflection in desired Wavelength ranges),
- Opto-Mechanical Design, Fabrication Configuration,
- Comprehensive Dimensional Metrology & Surface Characterization Laboratories,
- Customized System Assembly Setups
- Capable of AR Infrared coating, DLC Coating, Laser coating, Beam splitter coating, Neutral density filter coating, Interference filter coating, ITO conductive coating, High Reflective Coating such as Gold, Silver or Aluminium.